What does it take to run with the best in obtaining kernel processing scores that will optimize nutrition, health, and milk production in dairy cows? It takes a Kernel Processor unit: a good one. There are four key factors that need to be understood, implemented, and monitored to consistently crank out KP scores that will put you at the top of your dairy nutrition game.
1. Roll Condition
Farmers and custom operators take great pains to select the right rolls. And they should – it’s critical. An often overlooked factor in quality processing is the condition of the processing rolls. If rolls continue to be used when they pass their prime, KP scores begin to falter, then drop off sharply. Running a roll too long can actually be worse than choosing the wrong roll.
2. Tooth Spacing
Tooth spacing is the next critical factor in quality kernel processing. There are many different options in the marketplace.
- Running a tooth spacing combination of 4 grooves per inch on one roll and 4.5 grooves per inch on the other, is optimum for corn silage in the self-propelled industry.
- In direct-cut, whole-crop such as wheat, sorghum, etc., testing has shown 6 grooves per inch using a Fibertech Chevron roll with a straight tooth profile instead of a sawtooth profile, produced unmatched results in grain processing.
- For the feed mill industry, 10-groove rolls do a good crack on wheat, barley, etc. To just crack corn, 6-groove rolls are the most common, but 8 grooves can be used if you’d like to process it a bit finer.
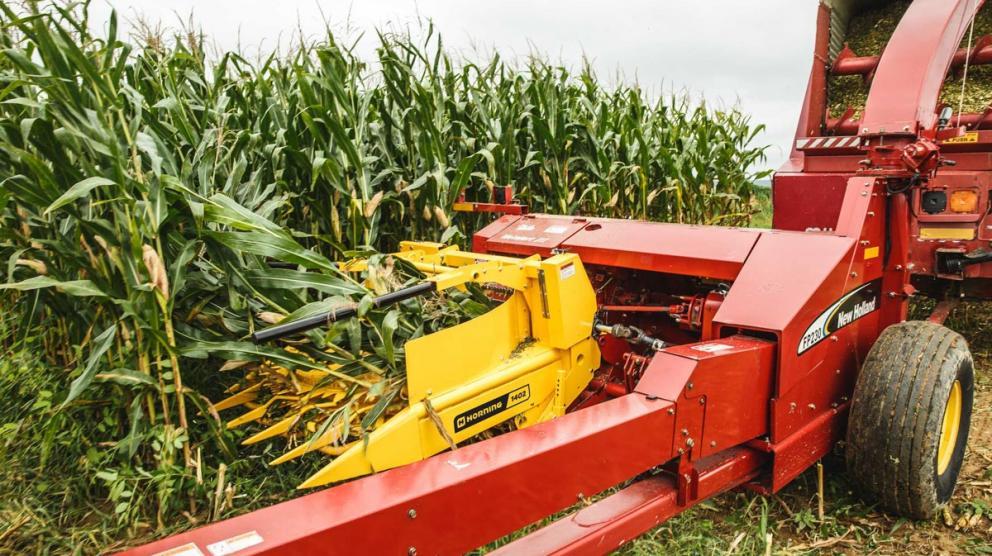
3. Tooth style
The third critical factor in outstanding kernel processing is the style of the tooth.
First a brief history of the development of tooth-style designs. Kernel Processing first debuted in the ’80s with straight tooth rollers. When processing took hold in the industry in the mid-’90s, innovation soon followed with the sawtooth design for more ripping action. The Hi-Capacity sawtooth design was pioneered by Horning in 2002. In 2007, Horning introduced Dual Cut (now being discontinued in favor of better designs) to the marketplace with great success. The design that Shredlage began using in 2011 is a similar variation of the dual cut design. A huge breakthrough came to the industry when Horning unveiled the innovative Fibertech Chevron design in 2015, a patented offering that continues to lead the market. What will be the next innovation? Stay tuned!
Tooth style contributes to quality kernel processing in 3 ways:
- Groove patterns affect the way the forage crop mat feeds through between the rolls. This affects wear life, crop mat penetration, and throughput capability.
- Tooth shape, formed by the intersecting lines running horizontally and vertically across the roll, is key to the type of processing action. Fibertech Chevron tooth shape has square corners and can be used with either the Hi-Capacity sawtooth profile or the straight tooth profile depending on the application. The shape and profile combination of the teeth have a huge bearing on how much ripping action happens, how the crop mat is penetrated, and how the wear pattern on the roll develops.
- Tooth quantity configurations can be chosen for different fineness in processing for various applications.
The more aggressive roll patterns are designed for higher throughput on higher horsepower machines and better processing.
4. Speed difference
The fourth critical factor (a driving factor) to quality kernel processing, is the speed difference at which the rolls are spinning. 20% differential was common in the early days but has been stepped up to 30% in most models. Today new machines are delivered with at least a 30% speed differential, and times in the self-propelled industry a 40% to 50% differential is common. This delivers the optimum processing action.
Some older machines will not be able to go more than 30% but quite a few can be updated. It simply takes more horsepower to do a better processing job. The higher the speed differential the more visible the results.